- Cost effective direct buried design
- Long maintenance free life span
- Variety of heights and classes
- Minimal vibration and deflection
- Resistant to corrosion
- High resistance to sulfate attack
- Environmentally friendly
- Varity of colours and finishes
- Resistant to rot, fire, and insects
- Hollow internal raceway
- Monetary – Eliminates the need for a costly anchor pole base footing.
- Time Savings – Faster installation, allowing more poles to be installed.
- Simple – No reliance on weather, form work, or pouring schedules.
- Appearance – No exposed base plates, or anchors bolts.
- Engineered – The pole and footing are continuous, forming a stronger structure.
- Environmental – Does not contaminate the soil, unlike direct buried wood poles which contain chemical treatments.
- Landscaping – Whether it be grass, concrete or asphalt, the surrounding ground is finished right up to the pole.
- Maintenance Free – Can be placed into the ground without the fear of rust or rot.
- Always store concrete poles on wood, ideally 2 x 6 hardwood, or similar wood which is finished enough to have opposite sides flat and parallel (no logs or branches). Never stack poles without proper spacing, a sufficient thickness should allow the placing of slings in between layers.
- The location of wood supports shall be placed 1/5 of the total length from each end. Minimum two wood supports for poles under 30 feet, and min. three (3) wood supports for poles over 30 feet.
- When poles are stored in more than one layer, each piece of wood support must be placed one above the other, so that the weight of the poles above is transmitted directly downward through each wood support and does not induce bending stresses on the poles.
- Store on a level surface. If the surface is not level, place extra supports to offset and balance the load properly.
- Place wedges on each of the wood supports, on round poles only, to prevent them from rolling.
- Poles should be aligned on top of each other to form a straight line.
- We only recommend nylon slings when handling concrete poles.
- In lifting the pole from a single pick-up point, use either a choker sling or a loop sling with one complete extra turn around the pole just above the balance point.
- We recommend using two pick-up points for poles over 40 feet, and choker-type attachment should be used on the pole.
- USI – Utility Structures Inc. company logo
- YEAR – the year of manufacture
- JOB – Special ID tracking number
- HT. – the overall height of the pole
- DATE – day of manufacture
- P – Signifies the pole is prestressed
- CL. – Pole Class (the strength of the pole)
- CSA – the use of the C.S.A. logo states that the pole is manufactured to Canadian Standards Association A.14.
- MADE IN CANADA – the country in which the pole was manufactured
Technical Information
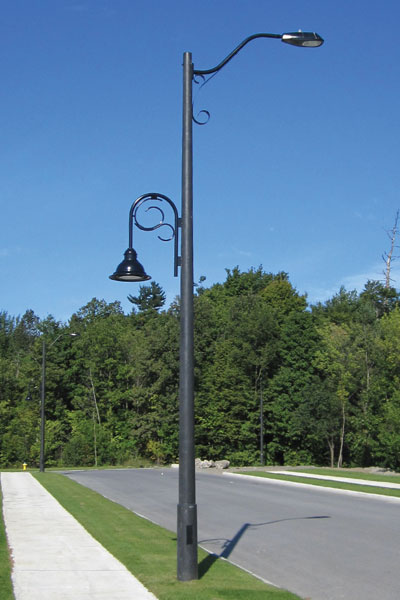
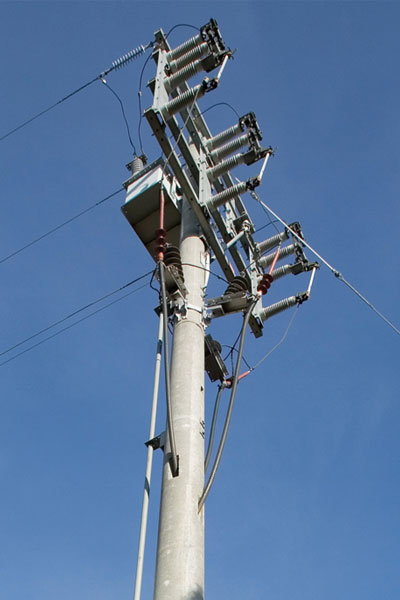
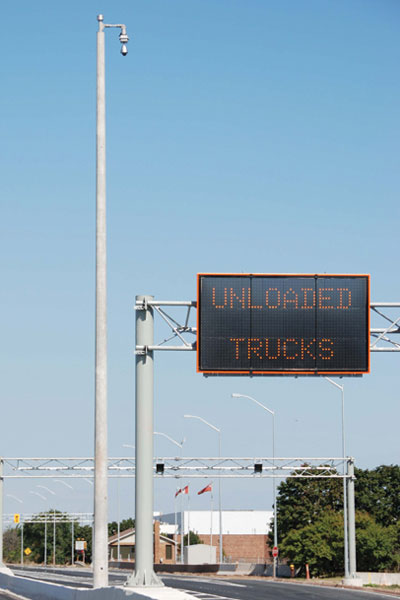
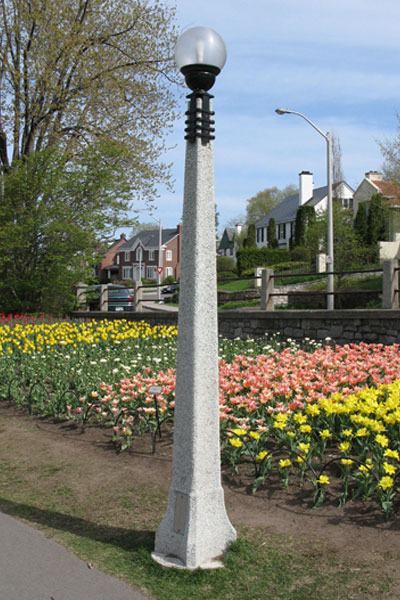
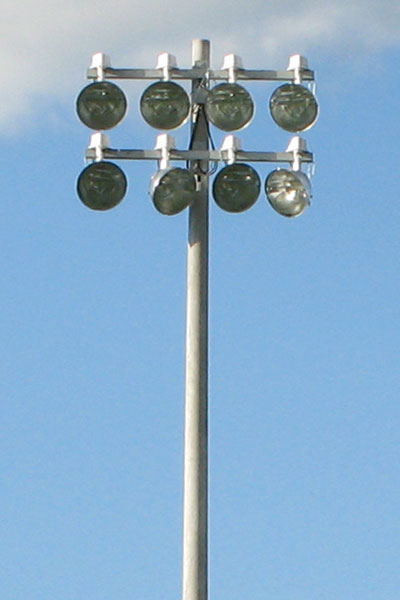
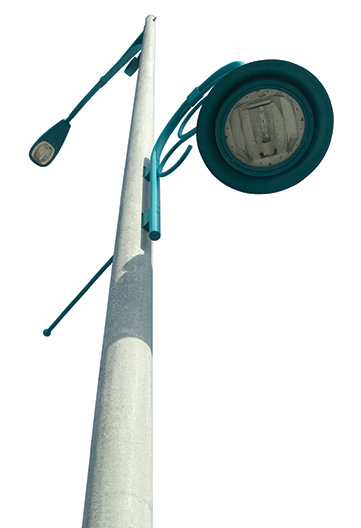
1. The Benefits of Concrete
Why Spun Concrete Poles?
Unlike conventional cast poles, prestressed spun concrete poles are centrifugally cast. This process involves spinning the poles at a very high rpm, which produces poles with the highest density and strength to weight ratio of any concrete available. As a result they are more durable; longer lasting and resistant to freeze/thaw cycles and chemical agents.
All our concrete pole are prestressed with high-tensile steel that is stretched before the concrete is cast, then released to maintain concrete compression. Prestressing greatly increases both the strength and resilience of the pole, providing far greater longevity than non-prestressed concrete poles.
In addition, the centrifugal (spinning) process creates a smooth, hollow raceway, tunnel inside the pole. This allows for internal routing of electrical cables.
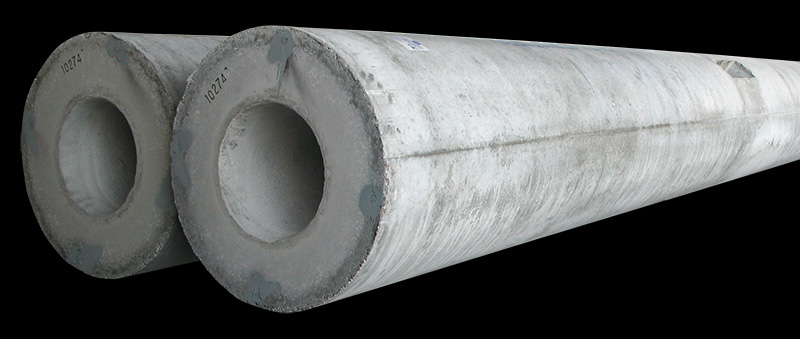
Consider the Advantages
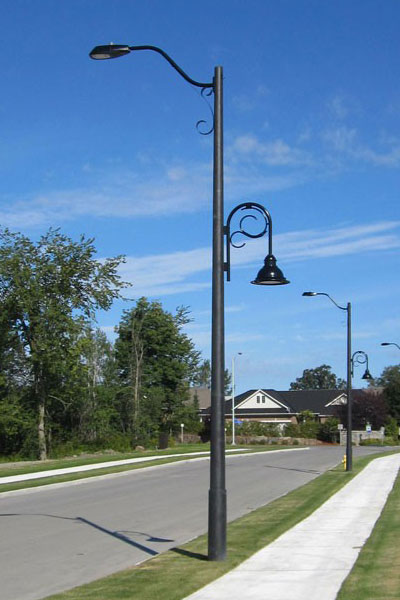
Design
Our prestressed spun concrete poles meet design criteria of the latest revisions of CSA A14 and ASTM C1089 standards. We are also an accredited CSA A23.4 certified precast plant.
Materials
Cement
Shall be high early (HE) strength and shall meet all physical requirements of CSA Standard A3000.
Reinforcing and Stressing Strands
Deformed reinforcing bars shall conform to CSA G30.18 and ASTM A615. Prestressing steel reinforcement shall conform to CSA G279 and ASTM A416. Helical reinforcing wire shall conform to ASTM A82. Galvanized or epoxy coated rebar is available upon request.
Aggregates
Coarse and fine aggregates shall meet all physical requirements of CSA standard A23.1. Aggregates shall be washed to achieve optimum quality.
Admixtures
Air entrainment, water reducers, corrosion inhibitors and accelerators shall conform to CSA A23.1. Air entrainment shall be used to produce 5-8% air content in the mix, which will improve the resistance to freeze/thaw.
Water
Shall be clear and free of any acid, alkali, sediment or organic matter.
Hardware
All Hardware and accessories shall be plated, hot dipped galvanized or stainless steel. Handhole frames & covers shall be manufactured using a high density zinc alloy.
All hardware such as inserts, fasteners, crossarms, pole steps, fin caps, and base plates shall be plated, hot dipped galvanized or stainless steel.
Pole Tops
All pole tops will be equipped with a weatherproof cap, except those with a tenon top or optional fin cap.
Simple and cost effective! The most common method and biggest advantage for installing a concrete pole is by direct embedment. The pole is placed into an augured hole lined with gravel then back filled with native soils, stone dust or cement (depending on the soil conditions).
Advantages of direct embedment:
Direct Embedment Installation Guidelines
Calculating the Depth of the Pole
Poles are typically set into the ground: 10% of the overall height + 2 feet, except in questionable soil conditions.
Example: Overall pole height: 30 feet, the pole should be buried: 3 feet + 2 feet = 5 feet below grade, and 25 feet above grade.
Note: always consult an engineer and review the soils report.
Calculating the Diameter and the Length of the Hole
Auger hole minimum 10 inches larger than the butt diameter of the pole, and an extra 6 inches deeper then the depth requirement.
Example: Overall pole height is: 35 feet and butt diameter is 14 inches, auger the hole Min: 24 inches in diameter and the depth 6 feet.
Depth Calculation: 35 feet X 10% = 3 feet, 6 inches plus 2 feet = 5 feet, 6 inches plus 6 inches for GA base = a total of 6 feet of augured depth.
The simple direct embedment method may not be suitable for all applications. When poles are in unstable soil conditions, or with large or unbalanced loads, either an engineered base or special backfill (i.e. concrete) may be required. USI can also supply concrete poles for the Base Plate or Socket Mounting methods.
Base Plate Mounting
Option B
Base Plate – Flush with Bolts Exposed
Option B1
Base Plate – Hidden Bolt Pockets
Option B2
Base Plate – Below Grade Stub
Socket Mounting
Socket Mounting may be installed flush to grade or poured at a desired height to act as extra protection from impact.
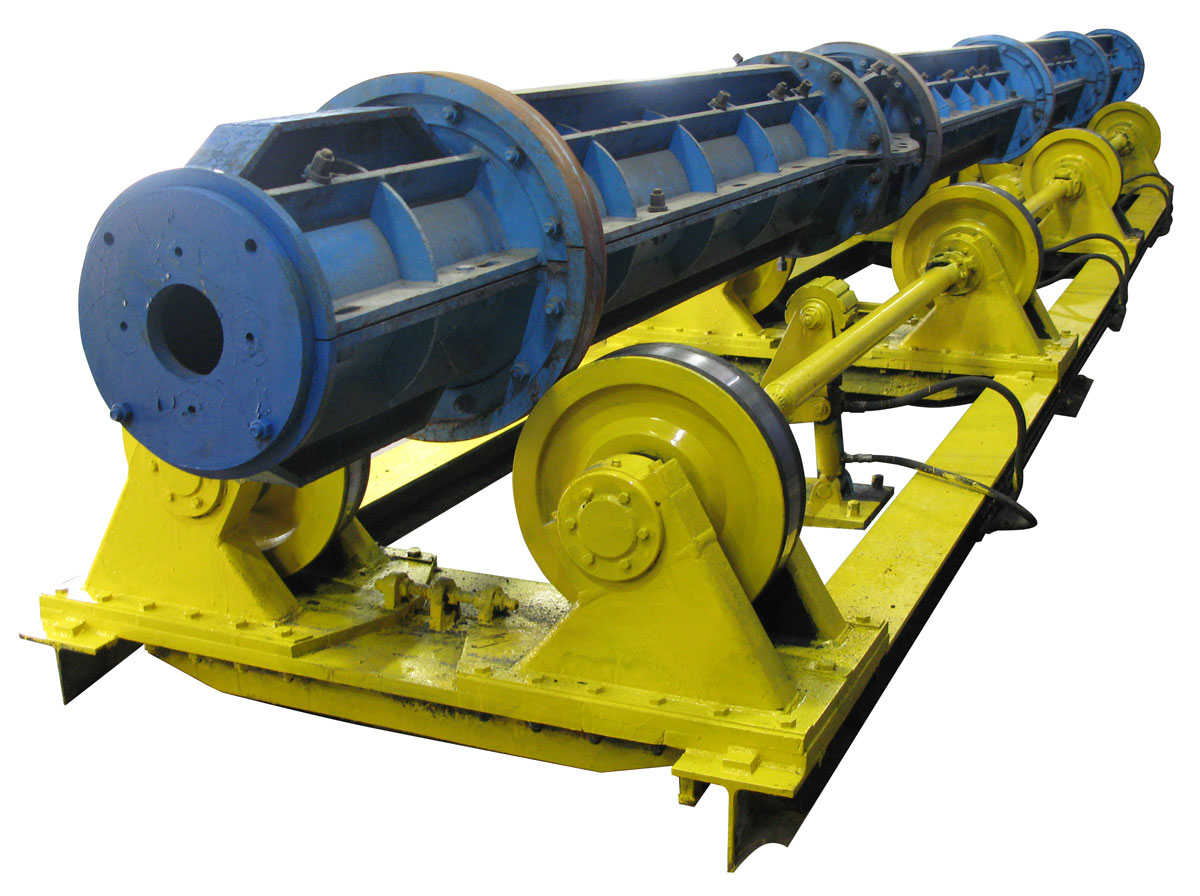
Molds
Only steel molds shall be used, with dimensions and cross sections as shown in our product catalogue. The reinforcing steel cage shall be centered and positioned in the mold by means of plastic spacers, to ensure a minimum concrete coverage of 3⁄4". The prestressing steel shall be stressed to a maximum of 70% of its ultimate capacity.
Concrete
The minimum 28-day cylinder strength for concrete used in poles shall be 50 MPa (7250 psi) for standard grey structural concrete, and 45 MPa (6525 psi) for architectural decorative concrete. The compressive strength of concrete mixes shall be established in accordance with CAN/CSA-A23.2-9C.
Centrifugal Spinning Process
The entire steel mold shall be spun utilizing the “Vibraspun” process, which is a four stage vibration spinning cycle. The length of time and speed required will vary based on the style of concrete pole.
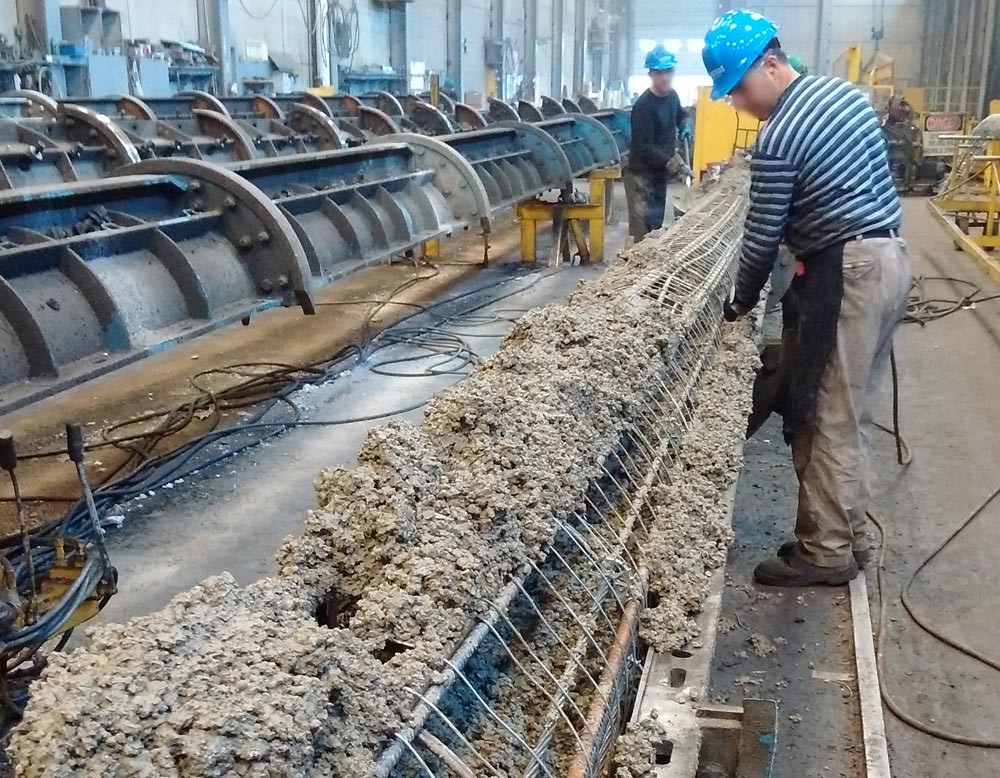
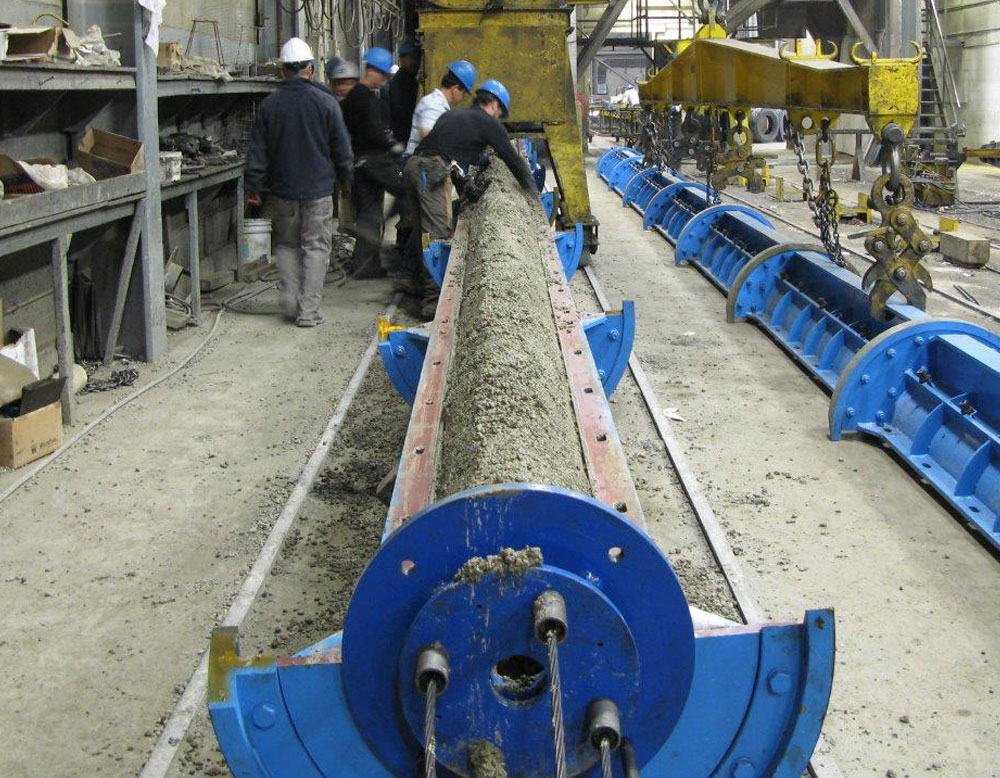
USI spun poles are made of high strength prestressed concrete, making them extremely durable and flexible. USI spun concrete poles are designed to withstand specific service loads and handling loads – with safety factors considered. But storage and handling practices are easily overlooked. Attention to the following details can help minimize damage.
Storage
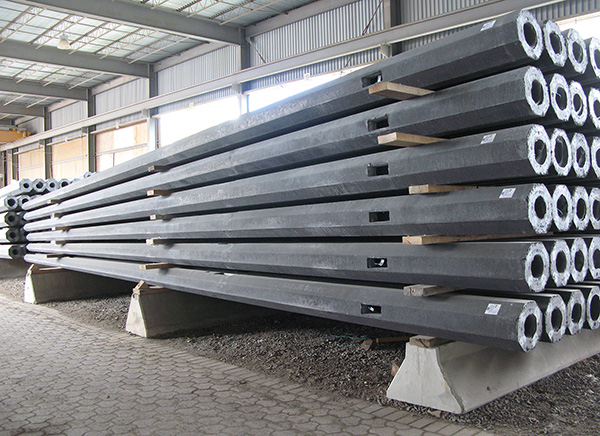
Handling
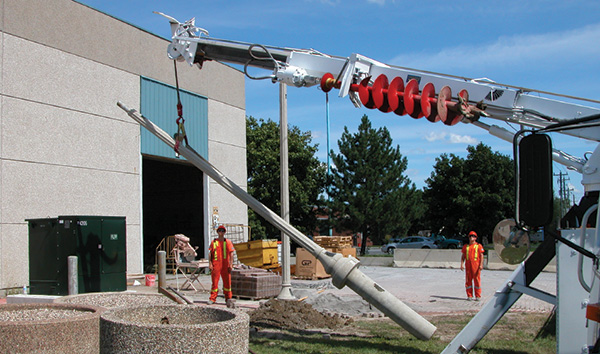
Round
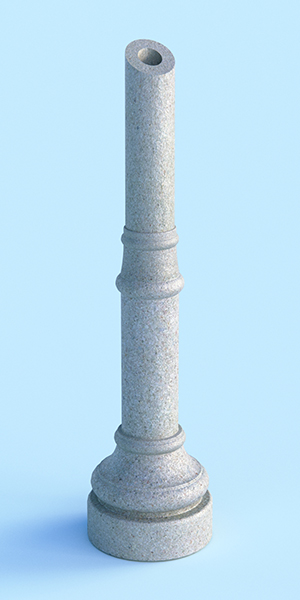
Astoria
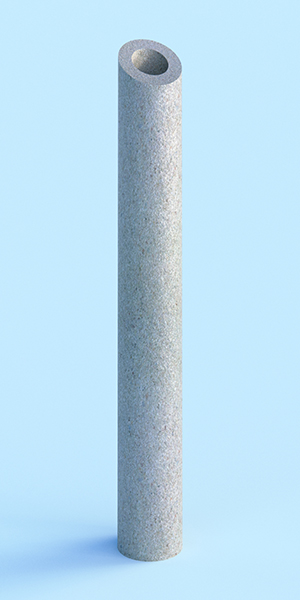
Hampton
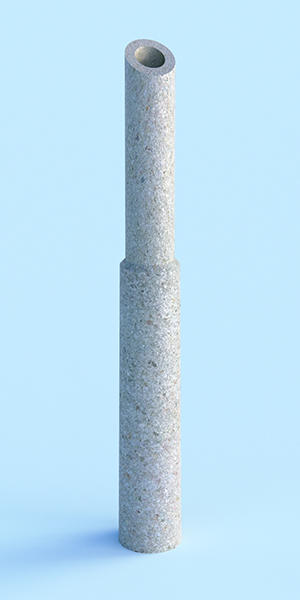
Newport
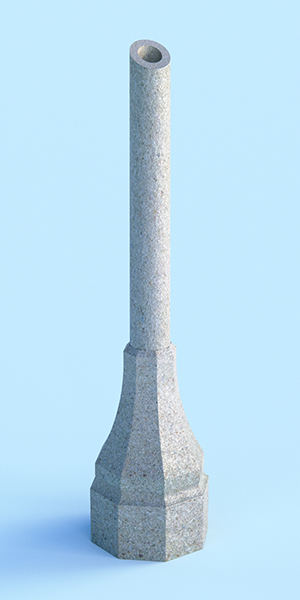
Rockcliffe
Octagonal
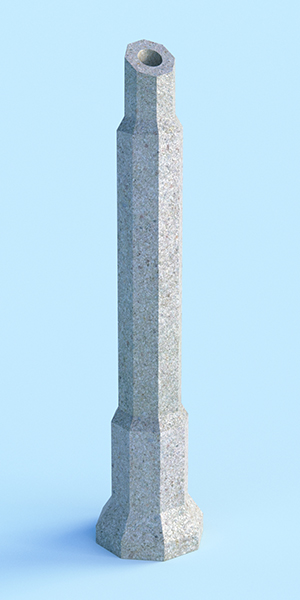
Cambridge
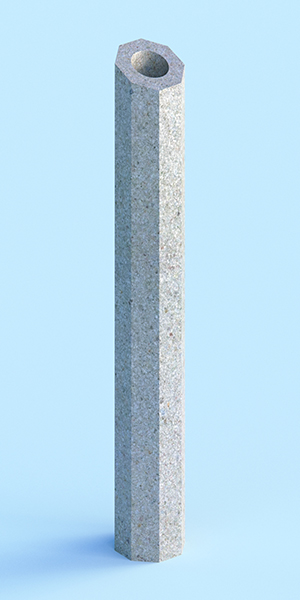
Madison
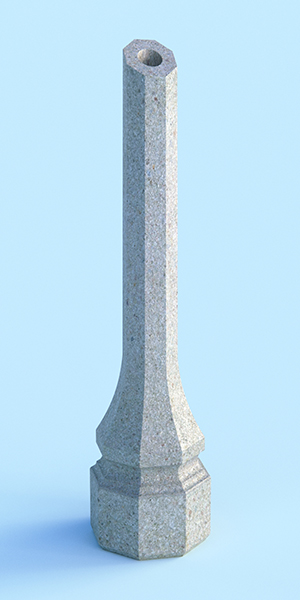
Parkdale
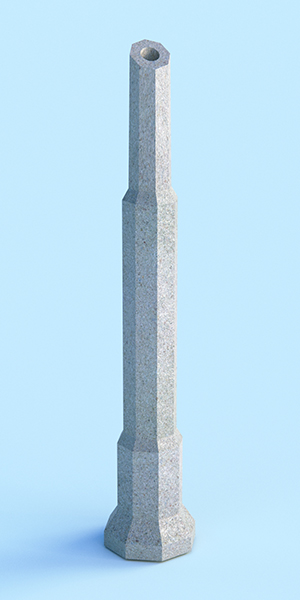
Stratford
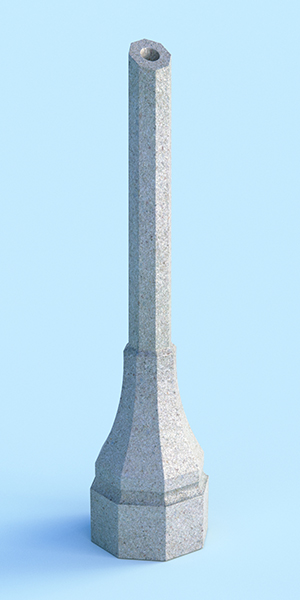
Westmount
Square
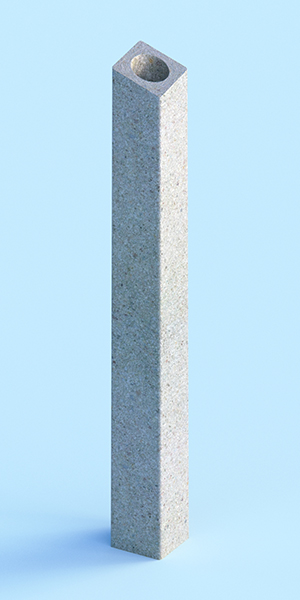
Oxford
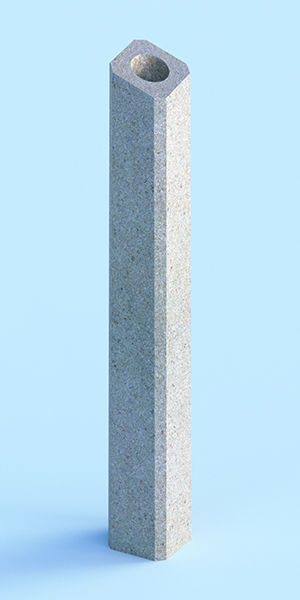
Thompson
Fluted
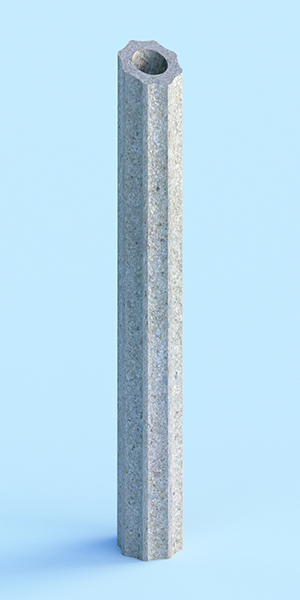
Astoria
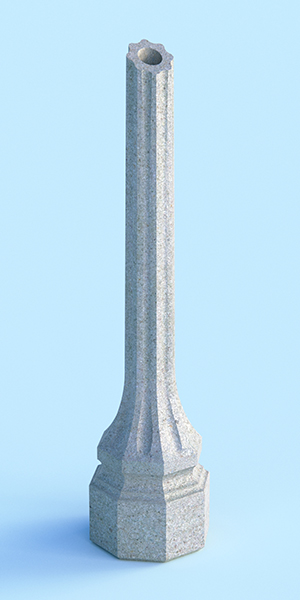
Grandview
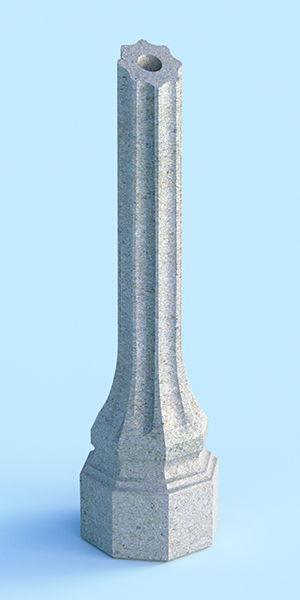
Victorian
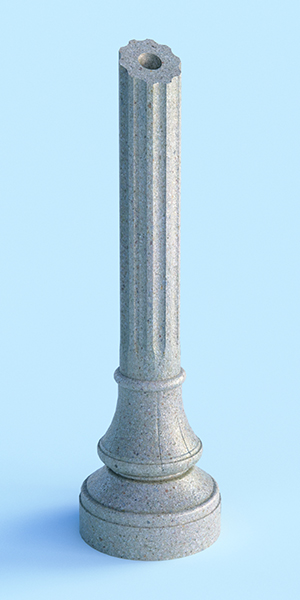
Washington
Finishes
USI offers 4 different finishes: mold, polished, etched and exposed. The Plain Grey Mold finish is a standard for all poles.
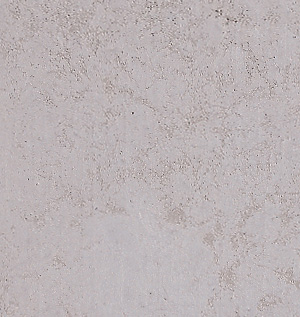
1 – Plain Grey
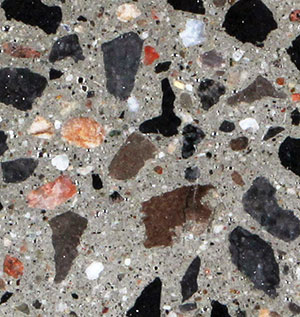
2 – Polished
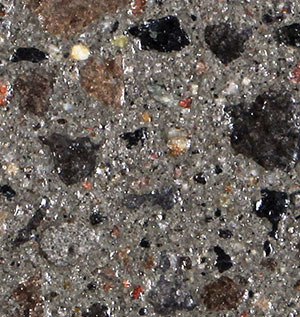
3 – Etched
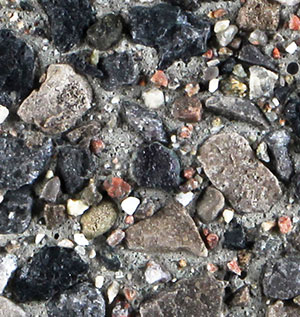
4 – Exposed
For more information on USI Finishes please visit our Finishes section.
Colours
USI offers 12 standard colour choices. Custom colours are available upon request.
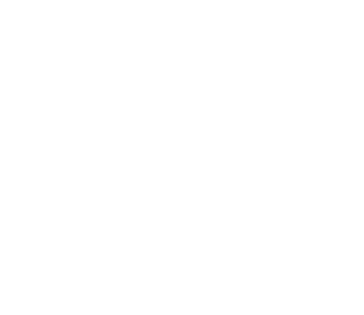
AR – Autumn Red
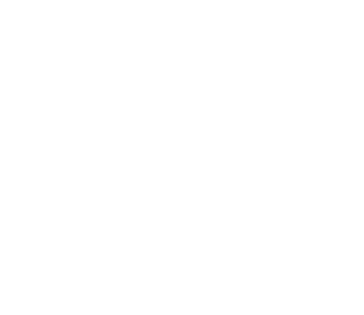
AJ – Aztec Jade
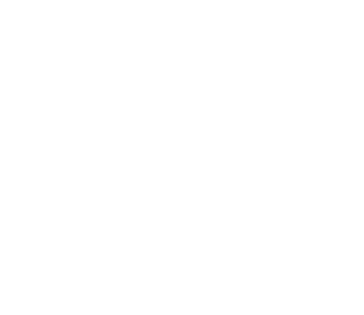
BE – Black Eclipse
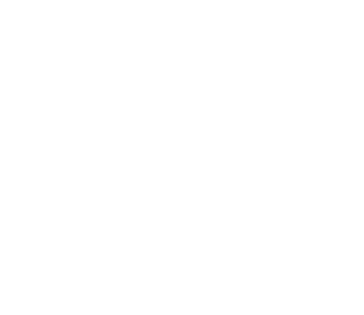
DB – Dark Bronze
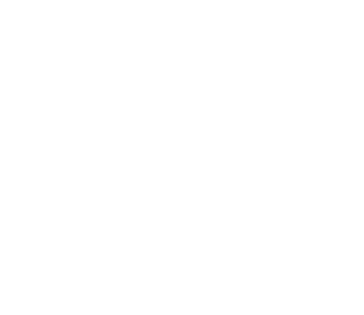
DR – Desert Rose
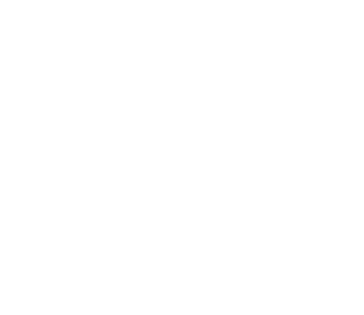
DS – Desert Sand
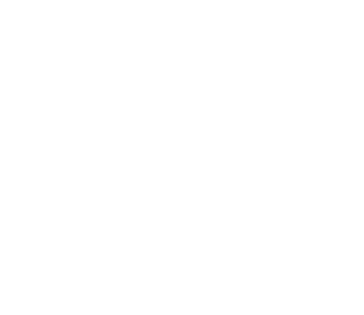
ML – Midnight Lace
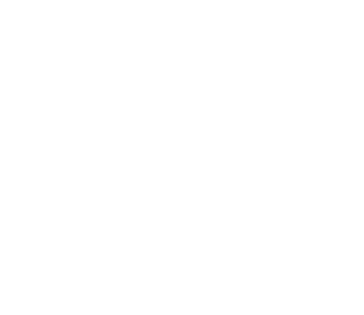
NG – Natural Grey
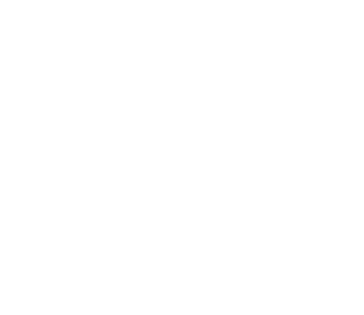
OJ – Oriental Jade
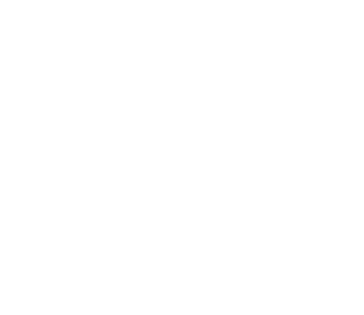
SP – Salt & Pepper
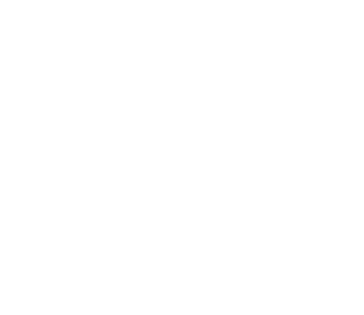
SB – Seluki Bronze
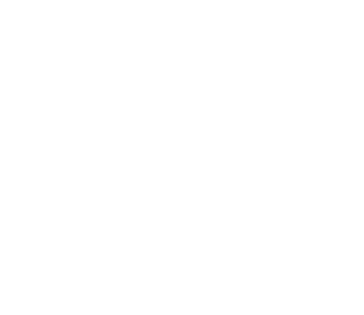
VW – Venetian White
For more information on USI Colours please visit our Colours section.
APole Top Aperture
Through the centrifugal casting process, our spun concrete poles achieve a hallow raceway ideal for placing wiring. Access holes (top & bottom) can be cast in for getting the wires in and out of this naturally formed conduit. One end of the holes is typically sloped to provide clear acess and the other is rounded to protect the wire during installation.
BBelow Grade Aperture
Through the centrifugal casting process, our spun concrete poles achieve a hallow raceway ideal for placing wiring. Access holes (top & bottom) can be cast in for getting the wires in and out of this naturally formed conduit. One end of the holes is typically sloped to provide clear acess and the other is rounded to protect the wire during installation.
CThrough Holes
Through holes for bolts are formed directly in the concrete. Size and position will vary according to fixture.
DCast In Threaded Inserts
Inserts shall be cast directly into the concrete pole when required for threaded bolts or attachments. All inserts shall be hot dipped galvanized, or zinc alloy for maximum protection. Inserts are designed to accept standard UNC bolts.
Standard inserts:
DIMENSION | INSERT DIAMETERS | |||
A | ||||
6mm [1/4"] | ||||
9mm [3/8"] | ||||
13mm [1/2"] | ||||
16mm [5/8"] |
||||
20mm [3/4"] |
Note: Inserts are designed to accept standard UNC bolts. Additional sizes are available upon request.
Pole attachments with inserts
All lighting bracket arms, pole steps and scroll arm attachments that are mounted to the pole using inserts, can only be torqued to a maximum of 20 ft. - lbs.
EIdentification Plate
Concrete poles are built to CSA Standard A.14. All poles come equipped with this nameplate, which also outlines nine important features of each pole.
FHandhole Boxes and Cover Plates
Handhole boxes are typically 36" above grade. Our Handhole boxes and covers are comprised of a die cast (ZA 12) zinc alloy. The cover is form fitting to the box which allows for ease of access.
Handhole Boxes
BOX NUMBER | DIMENSIONS | ||
A | B | C | |
1 | 50mm [2"] | 200mm [8"] | 45mm [1 3/4"] |
2 | 63mm [2 1/2"] | 200mm [8"] | 50mm [2"] |
3 | 81mm [3 1/2"] | 263mm [10 1/2"] | 63mm [2 1/2"] |
Cover Plates
COVER NUMBER | DIMENSIONS | ||
X | Y | Z | |
1 | 56mm [2 1/4"] | 225mm [9"] | 3mm [1/4"] |
2 | 70mm [2 3/4"] | 225mm [9"] | 3mm [1/4"] |
3 | 170mm [3 3/4"] | 288mm [11 1/2"] | 3mm [1/4"] |
GStainless Steel Screws
Handhole Covers are fastened with stainless steel (18-8), button head cap screws. They are available in the following two head styles; Hex head, and Tamper proof hex head.
HIElectrical Grounding
CSA requires at least one ground connection providing adequate electrical contact to one steel rod. The ground bar is continuous throughout the length of the pole and metallically connected to all other reinforcing rods. Grounding will consist of a #6 bare copper strand. The following two methods are approved by CSA:
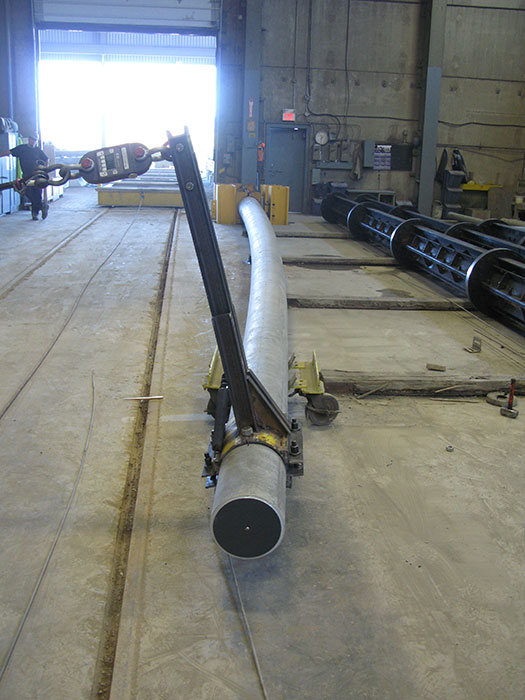
Quality Control
With over 50 years in the precast industry USI has developed a reputation for high quality products. As an accredited CSA A23.4 certified plant, we must maintain a quality control program. This compliance control program assures the product is inspected according to the industry's best production practices.
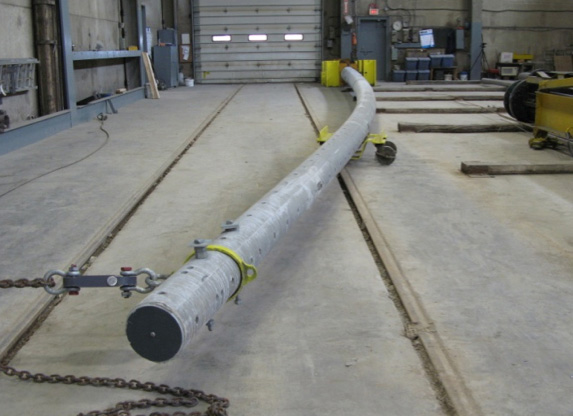
Every pole carries a unique ID numbered tagging system which ensures traceability of all components and manufacturing procedures for that pole. The concrete mix is tested regularly to CSA standards. A Quality Control technician inspects and approves the pole through each stage, and a final inspection and stamp are required after the entire manufacturing process is completed.
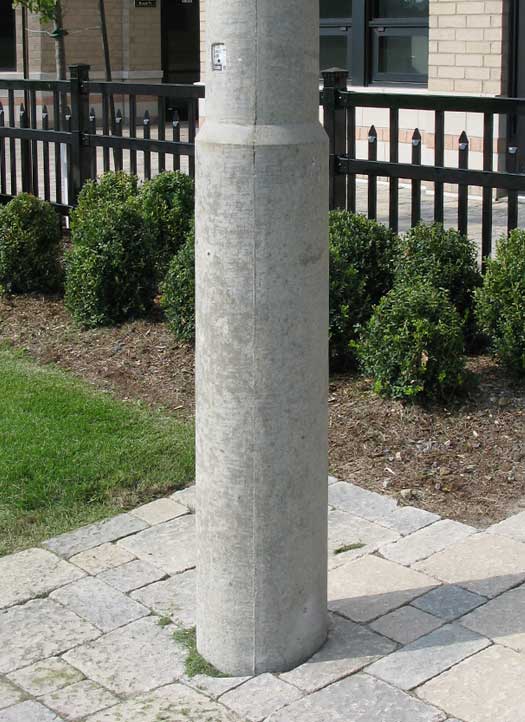
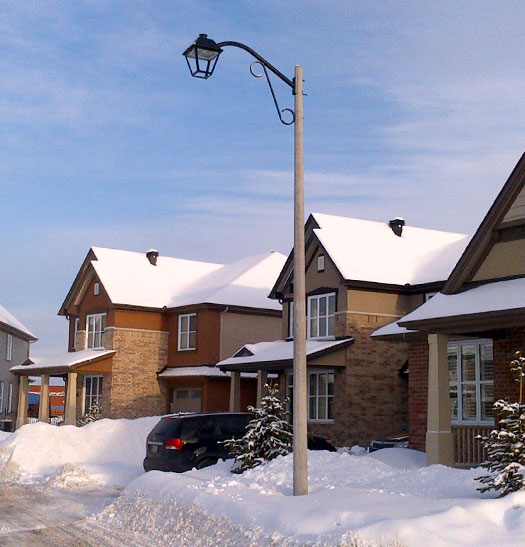
Utility Structures Inc. 10-Year Warranty
Utility Structures Inc. warrants its products against defects in material and workmanship. Without charge Utility Structures Inc. will either repair or replace any properly installed Utility Structures Inc. product which fails under normal operating conditions within a ten (10) year period from the date of shipment, providing our inspection determines it to be defective under the terms of this warranty. Utility Structures Inc. reserves the right in its solo discretion to decide between repair and replacement.
This warranty covers only products manufactured by Utility Structures Inc. and does not extend to transportation or installation charges, nor does it apply to any equipment of another manufacturer used in conjunction with Utility Structures Inc. products. This express warranty is in lieu of all other representations, warranties or conditions expressed or implied. In no event shall Utility Structures Inc’s liability under this warranty exceed the amount paid by the customer to Utility Structures Inc. and in no event shall Utility Structures Inc. be liable for any special, indirect or consequential damages.
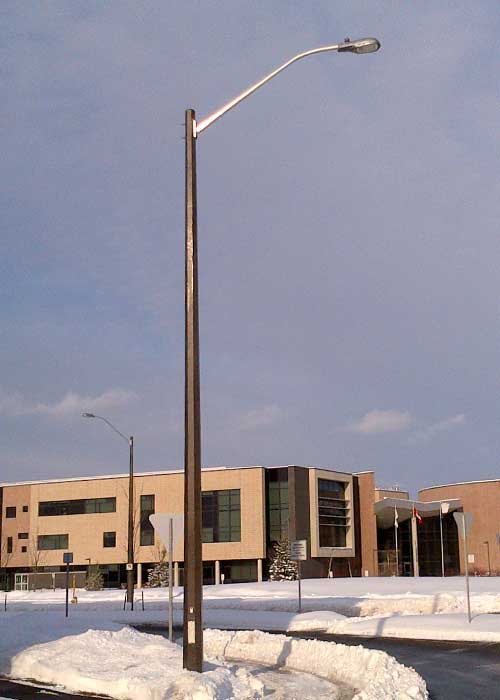

We currently expect our spun concrete poles to have a life expectancy of fifty (50) years or more. Through new concrete technology, advanced manufacturing processes, and stringent quality control we can assure the client of this long life.
Address
61 Bongard Avenue
Ottawa, Ontario, Canada
K2E 6V2
Phone
Toll Free: 1-800-267-6466
Tel: (613) 225-6398
Fax: (613) 225-1681
Sales: sales@utilitystructures.com
Info: info@utilitystructures.com
Business Hours
Monday – Friday:
8:00 a.m. – 5:00 p.m. (EST)